Is there a single material capable of revolutionizing insulation, sealing, and bonding across diverse industries, from construction to DIY projects? The answer, unequivocally, is yes: polyurethane foam. Its adaptability and unique properties have solidified its place as an indispensable component in countless applications.
Polyurethane foam, a testament to material science's ingenuity, has swiftly moved beyond its humble beginnings to become a cornerstone of modern construction, manufacturing, and even everyday household tasks. This remarkable substance, characterized by its versatility and efficiency, offers an array of benefits that make it a preferred choice for professionals and homeowners alike. Understanding its composition, applications, and advantages is key to appreciating the true scope of this groundbreaking material.
Feature | Description |
---|---|
Composition | Polyurethane foam is a polymer formed by the reaction of a polyol and an isocyanate. The reaction is catalyzed and often includes other additives to modify its properties. |
Structure | It can exist in both open-cell and closed-cell structures. Closed-cell foam provides superior insulation and moisture resistance, while open-cell foam is often used for sound absorption. |
Applications | Wide-ranging, including insulation (walls, roofs, pipes), sealing gaps, filling voids, packaging, automotive components, furniture, and specialized uses like flotation devices. |
Advantages | Excellent thermal insulation, air sealing, moisture resistance, durability, lightweight, versatility, and ease of application. |
Types | Available in various forms: spray foam, expanding foam, rigid foam boards, flexible foams, each suited to specific applications. The type of foam is selected based on the desired properties. |
Environmental Considerations | Modern polyurethane foams are often formulated to be more environmentally friendly, with options that use blowing agents with lower global warming potential. |
At its core, polyurethane foam is a plastic and porous material created through a chemical reaction involving polyols and isocyanates. This reaction is often catalyzed and may include additives that modify the foam's characteristics, allowing for customization to suit specific needs. The resulting material can exist in either open-cell or closed-cell structures, each offering distinct advantages.
Closed-cell foam excels in insulation, creating a barrier against both heat and moisture. Its structure comprises individual, sealed cells, effectively trapping air and minimizing heat transfer. This characteristic makes it ideal for use in walls, roofs, and other areas where superior insulation is paramount. The closed-cell structure also resists water penetration, preventing moisture damage and prolonging the lifespan of the building or structure.
Conversely, open-cell foam offers excellent sound absorption properties. Its interconnected cells allow sound waves to pass through and dissipate energy, making it a popular choice for soundproofing applications in recording studios, home theaters, and other environments where noise reduction is essential.
The versatility of polyurethane foam extends far beyond its structural composition. Its diverse applications span numerous industries and everyday scenarios. In construction, it's a go-to for insulating walls, roofs, and foundations. It effectively seals gaps and cracks, preventing air leaks and improving energy efficiency. In packaging, it protects delicate items during shipping and handling. It's found in furniture, bedding, and automotive components, offering cushioning, support, and comfort.
The advantages of polyurethane foam are numerous and compelling. Its exceptional thermal insulation capabilities significantly reduce energy consumption, lowering heating and cooling costs. Its ability to create an airtight seal prevents drafts and moisture intrusion, contributing to a healthier and more comfortable indoor environment. The material's durability ensures a long lifespan, reducing the need for frequent replacements. Furthermore, its lightweight nature makes it easy to handle and install, streamlining construction and renovation projects.
The selection of polyurethane foam depends entirely on the application at hand. Spray foam, applied using specialized equipment, is a popular choice for insulating large areas, such as walls and roofs. Expanding foam, available in aerosol cans, is ideal for filling small gaps and cracks, providing a quick and easy sealing solution. Rigid foam boards, pre-cut and easy to install, are commonly used for insulation in walls and floors. Flexible foams find applications in furniture and cushioning, providing comfort and support.
The application process itself varies depending on the type of foam and the specific task. Spray foam projects require professional expertise and specialized equipment to ensure proper installation and performance. Expanding foam is typically applied using a dispensing gun or straw, and it expands rapidly upon application, filling the desired space. Rigid foam boards are cut to size and secured in place using adhesives or mechanical fasteners. Regardless of the application method, careful attention to detail and adherence to manufacturer's instructions are crucial to achieving optimal results.
The specific properties and features of polyurethane foam can vary depending on its intended application. For instance, in construction, the foam is often designed to meet stringent fire safety standards. Flame-retardant additives are incorporated to reduce the risk of fire spread and enhance occupant safety. In applications exposed to the elements, the foam may be formulated to resist moisture, UV radiation, and other environmental factors, ensuring long-term durability.
The use of polyurethane foam is not without environmental considerations. The production process can involve the use of potentially harmful chemicals. However, significant advancements have been made in recent years to develop more environmentally friendly formulations. Many manufacturers now offer polyurethane foams that use blowing agents with lower global warming potential, reducing their environmental impact. Responsible disposal and recycling practices are also important considerations.
The rise of polyurethane foam underscores the power of materials science. By understanding its composition, properties, and applications, one can harness its potential to create more energy-efficient buildings, improve product performance, and enhance everyday living. From the insulation in your home to the packaging that protects your online purchases, this versatile material is silently at work, improving the world around us.
When considering polyurethane foam for a project, it’s essential to choose the right type and application method. Factors such as thermal resistance (R-value), air sealing capabilities, and fire resistance should be considered. Consulting with professionals and researching the specific requirements of the project will help ensure that the best possible results are achieved. The use of personal protective equipment (PPE), such as gloves, eye protection, and respirators, is crucial during application to minimize exposure to chemicals.
The future of polyurethane foam promises further innovation and advancements. Researchers continue to explore new formulations, applications, and manufacturing techniques. The goal is to create more sustainable, durable, and efficient materials that can meet the evolving needs of a rapidly changing world. This commitment to innovation ensures that polyurethane foam will continue to play a pivotal role in shaping a better future.
The use of spray polyurethane foam (SPF) has become increasingly common. This method involves spraying the foam onto a surface, where it expands and solidifies. The process requires specialized equipment, typically a high-pressure system that mixes two components: polyol and isocyanate. The mixture is then sprayed onto the desired surface, forming a continuous, seamless layer of insulation and air barrier. SPF is particularly effective in irregular spaces and areas with complex geometries, providing a tight seal and maximizing insulation efficiency. Systems like the GRACO Reactor E-XP2 are often employed for professional-grade applications, capable of delivering the foam at high pressures and temperatures (up to 70°C) for optimal performance. The resulting monolithic layer adheres firmly to the substrate, eliminating gaps and minimizing thermal bridging.
The versatility of polyurethane foam is exemplified by its various types, each suited for specific needs. For instance, some foams are specifically designed for fire resistance, crucial in building construction to meet safety standards. Others are engineered to withstand extreme temperatures or high humidity, making them ideal for use in challenging environments. The choice of foam depends heavily on the intended application, with factors such as the required insulation value, the presence of moisture, and the anticipated exposure to the elements influencing the decision.
The role of polyurethane foam extends to DIY projects, where expanding foams are particularly useful for sealing gaps around windows and doors, filling cracks in walls, and adding insulation to hard-to-reach areas. These products come in convenient aerosol cans, making them easy to apply without specialized equipment. However, it's important to follow the manufacturer’s instructions carefully and use appropriate protective gear.

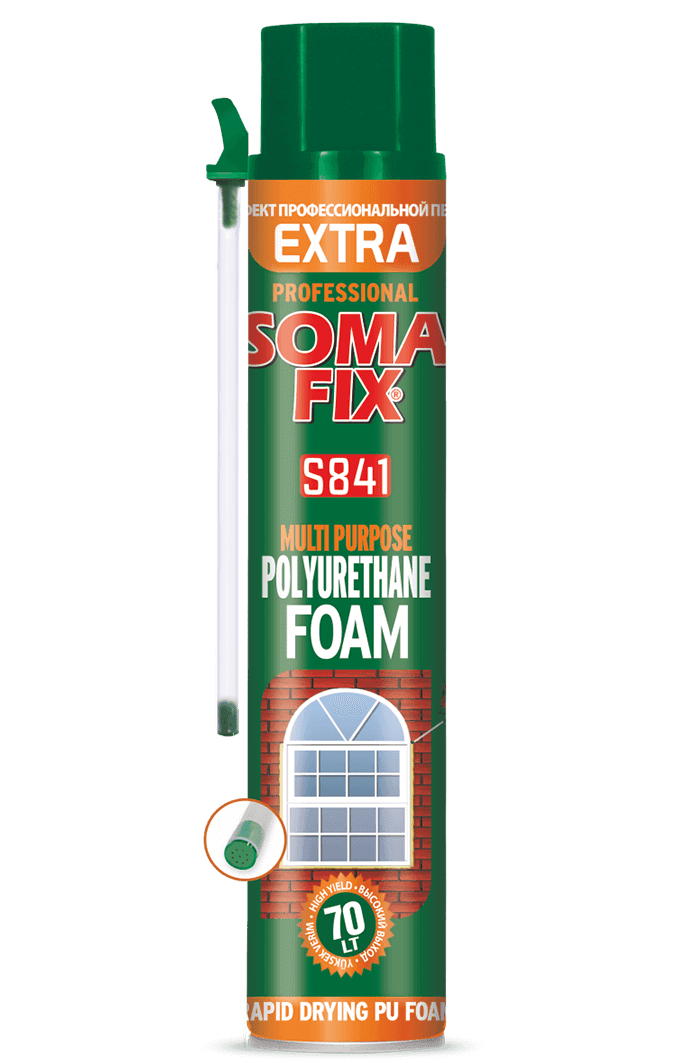